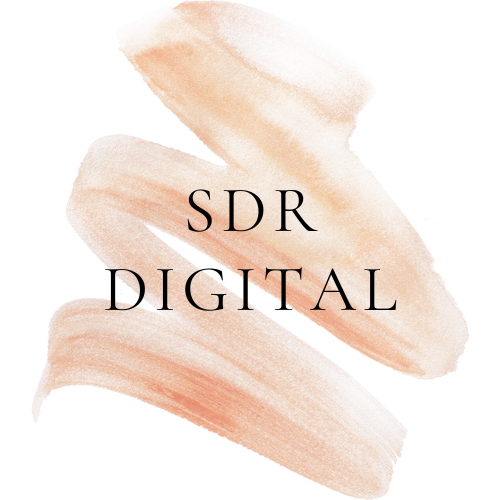
Continuous Improvement.
​
Every organisation, regardless of what industry they are in, is considering or running a Continuous Improvement Programme of some sort to improve performance and enable their people to contribute with their ideas and problem-solving skills. However, even with the best intentions, the unfortunate truth is that most efforts ultimately fail to fully meet expectations or lead to sustainable culture change
​
With wide experience across multiple industries, our consultants can support and guide you in establishing and running your Continuous Improvement strategy and programme, including leadership development, Lean Six Sigma training, PMO formation, project selection, communications strategy, change management capability, Lean Management Systems and recognition systems which all combine to help align your people around your strategic vision. Our experience as leaders, practitioners and coaches will help you embed new mindsets and behaviours, establish new systems of working and engage your people in improving processes to enable results and your journey to excellence
​
If you would like to find out more about Continuous Improvement Programmes and how they could help you and your organisation, then please feel free to contact us. You can do this by clicking on the button below and we will be happy to help.

Kaizen Cycle.
Kaizen is an approach for Continuous Improvement.
​
Kaizen is an approach to creating continuous improvement based on the idea that small, ongoing positive changes can reap significant improvements.
Typically, it is based on cooperation and commitment and stands in contrast to approaches that use radical or top-down changes to achieve transformation. Kaizen is core to lean manufacturing and the Toyota Way.
It was developed in the manufacturing sector to lower defects, eliminate waste, boost productivity, encourage worker purpose and accountability, and promote innovation.

Kaizen cycle for Continuous Improvement.
​
Kaizen can be implemented in a seven-step cycle to create an environment based on continuous improvement. This systematic method includes:
​
-
Get employees involved. Seek the involvement of employees, including gathering their help in identifying issues and problems. Doing so creates buy-in for change. Often, this is organized as specific groups of individuals charged with gathering and relaying information from a wider group of employees.​
​
-
Find problems. Using widespread feedback from all employees, gather a list of problems and potential opportunities. Create a list if there are many issues.
​​
-
Create a solution. Encourage employees to offer creative solutions, with all manner of ideas encouraged. Pick a winning solution or solutions from the ideas presented.
​​
-
Test the solution. Implement the winning solution chosen above, with everyone participating in the rollout. Create pilot programs or take other small steps to test out the solution.
​​
-
Analyze the results. At various intervals, check progress, with specific plans for who will be the point of contact and how best to keep ground-level workers engaged. Determine how successful the change has been.
​​
-
Standardize. If results are positive, adopt the solution throughout the organization.
​
-
Repeat. These seven steps should be repeated on an ongoing basis, with new solutions tested where appropriate or new lists of problems tackled.