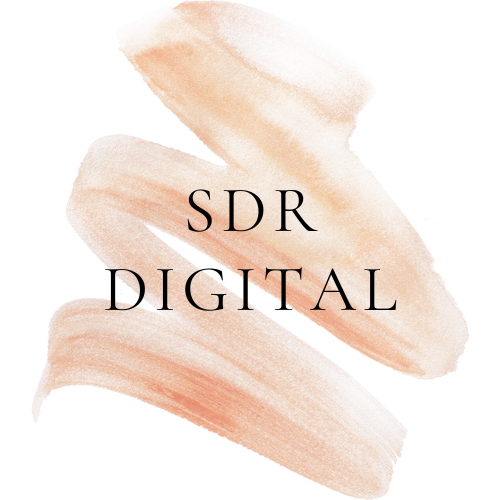
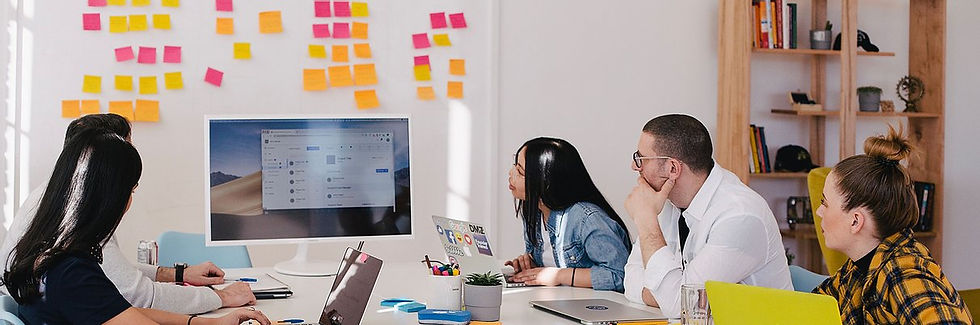
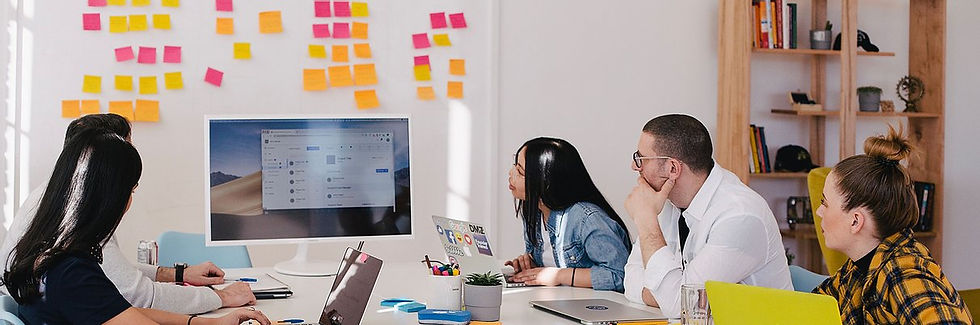
Lean Management Systems
Why do Lean Management Systems help our clients?
Lean cultures grow from Lean Management, and so establishing systems of management with the associated disciplines, routines and behaviours enable leaders and managers to set the tone, role model ideal behaviours and ensure the principles of Lean thinking become embedded in the ways of working.
Lean Management Systems also enable leaders to act as coaches, raising the capability of individuals and teams across the organisation, delegating decision-making authority and encouraging experimentation and learning according to the “fail fast” philosophy. Thus CI and problem-solving become a natural daily activity at every level of the organisation, and are not restricted to a ‘programme’ or to specific projects, so results improve in sustainable ways.
What is it?​
​
A Lean Management System is a key way of sustaining and extending continuous improvement in operations by engaging everyone, including leaders and managers, in focusing on process. This involves a culture change which can be very challenging. Lean Management Systems establish new routines and habits which make it easy for people to do the right thing, and difficult to do the wrong thing. When the fruits of these systems become apparent (“The right process will produce the right result”), then mindsets and behaviours change accordingly.
Lean Management Systems are an integration of Visual Management, Tiered Meetings, Daily Accountability, scientific Problem-Solving and Leader Standard Work which help organisations focus on process and deliver sustainable continuous improvement.
​
​
​
How do we do it?
Our approach will be to work with leadership teams and the wider organisation to build Lean Management Systems in a structured fashion. We start with the deployment of business strategy, ensuring a logical translation of strategic priorities into relevant goals, KPI measures and targets at every level of the organisation. Then at each level, one ‘segment’ at a time, we help the teams design and test a visual management performance board, iterating and adapting in PDCA (Plan-Do-Check-Act) fashion.
​
The purpose of these boards, consistent with Visual Management generally, is to enable everyone to see at a glance if we’re winning or losing across a balanced set of relevant goals, standards and KPI measures… “see together, understand together, act together”.
To promote interaction with these boards our consultants support the establishment of daily huddle meetings: these are 10-minute stand-up huddles around the team board focusing on exceptions, actions and follow-up with the intent that problems are solved at the lowest level possible. Under expert guidance and coaching will help improve leadership, communication, collaboration and problem-solving skills.
​
Finally, we can help with the implementation of Leader Standard Work, enabling leaders and managers to spend time at the Gemba, role-model Lean Leadership behaviours, exhibit the discipline of following standards, remove road-blocks and support the teams in continuous improvement. These activities themselves are subject to Visual Management promoting transparency, trust, accountability and making any exceptions stand out clearly.
If you would like to find out more about Lean Management Systems and how they could help you and your organisation, then please feel free to contact us. You can do this by clicking on the button below and we will be happy to help.
​